Content
- Advantages and Disadvantages of Conversion Cost
- Conversion Cost – Meaning, importance, Formula and More
- Difference between prime cost and conversion cost
- Total Period Cost Formula
- How to Calculate Variable Contribution Margin
- THE CRITICAL ROLE OF CONVERSION COST AND COMPARATIVE ADVANTAGE IN MODELING AGRICULTURAL LAND USE CHANGE
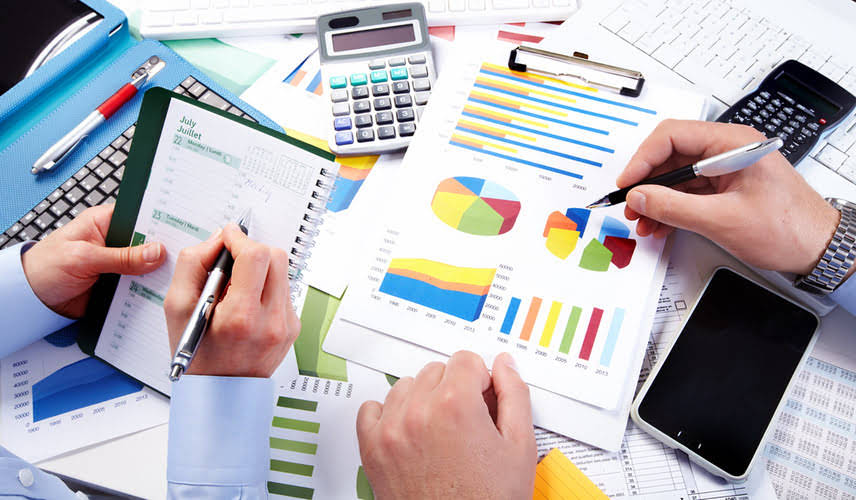
All such information is provided solely for convenience purposes only and all users thereof should be guided accordingly. However, if there are other expenses that are directly attributable to a product, then include them in the formula.
- These are the concepts of equivalent units and conversion costs.
- Conversion cost, as the name implies, is the total cost that a manufacturing entity incurs to transform or convert its direct materials into salable or finished product.
- Examples of direct labor workers include welders, machine operators, assemblers and painters etc.
- Typically, it is equal to the sum of entity’s total direct labor cost and total manufacturing overhead cost. https://www.tencon2022.org/
- These direct labor costs are the same ones used in calculating the prime cost in manufacturing.
- The company wants to know its conversion cost from the following mentioned information.
But you can search and find ways to determine an impressive conversion cost for your business. As we discussed, people commonly refer to conversion cost as cost per conversion. Between CPC and cost per click, which is an entirely different metric. The conversion cost tells you how much you are spending on average to convert one customer. Note that the spend we are talking about is the marketing spend. Also, this cost is commonly referred to as cost per conversion .
FundsNet requires Contributors, Writers and Authors to use Primary Sources to source and cite their work. These Sources include White Papers, Government Information & Data, Original Reporting and Interviews from Industry Experts. Reputable Publishers are also sourced and cited where appropriate. Learn more about the standards we follow in producing Accurate, Unbiased and Researched Content in our editorial policy. The following are some of the expenses that a business will incur. It’s mainly useful for setting the appropriate price of a product. They don’t have to be directly traceable to a certain product.
Advantages and Disadvantages of Conversion Cost
It is the direct labor plus any manufacturing overheads needed to convert raw materials into a finished product. For this reason, they are sometimes referred to as fixed costs. Overhead costs are included in the calculation of a business’s conversion costs, specifically as those overhead costs are necessary to the transformation of raw materials into finished products. The cost of direct labor is included in both prime and conversion costs. The calculation for prime costs includes direct labor, plus the amount spent on direct materials. The calculation for conversion costs also includes direct labor .
Each individual’s unique needs should be considered when deciding on chosen products. A lot of cost data were gathered above, but not all of them count as conversion costs. Finally, we will be doing some exercises to deepen our understanding of conversion costs. In this article, we will be discussing what conversion costs are. For example, the raw materials for bread, which are typically eggs, flour, and yeast, don’t convert into bread on their own.
Conversion Cost – Meaning, importance, Formula and More
Ideally, the cost per conversion will go down when you make changes to your campaign. This means that the company had a total of $130,000 in conversion costs in January. The company was able to produce 25,000 units of product in the same month. The conversion cost per unit for the month of January was $5.20 ($130,000 in conversion costs divided by 25,000 units produced equals 5.2). To make the frames for the glasses, workers must cut the appropriate length of material and then shape the material into the frame with the help of a frame mold. At the end of every year, after the firm’s inventory count, the firm looks at production costs.
- The calculation of prime costs also helps organizations set prices at a level that produces an acceptable amount of profit.
- For example, previous interactions with your brand can play a role.
- If some costs are not reaping desired output, these are identified as waste and eliminated by restructuring the process.
- Conversion cost is often used by operations managers to determine if there is any waste in the production process.
- Conversion cost also helps managers to identify waste and assess the efficiency of the production process.
For example, the salaries of the employees who are responsible for manufacturing goods, such as machinists or assembly-line workers, are considered direct labor costs. If you hire contract workers for a particular project, the wages you pay them would also be counted as direct labor expenses.
Or they don’t spend enough on campaigns that have the potential. First, it gives a boost to your campaigns that are already delivering. Second, not all your competitors will be as proactive as this.
Balance SheetA balance sheet is one of the financial statements of a company that presents the shareholders’ equity, liabilities, and assets of the company at a specific point in time. It is based on the accounting equation that states that the sum of the total liabilities and the owner’s capital equals the total assets of the company. Means the expenses directly attributed to each unit of product or the process. These include electricity bills, rent, depreciation, plant insurance, repairs and maintenance of plants, etc.
If your garage conversion is part of a larger renovation, water-fed underfloor heating will be cheaper to run over time, if more expensive to install initially. The prime cost figure is also helpful https://www.bookstime.com/ in setting the price at such a level that can easily generate enough profit for the company. Being on your toes and constantly chopping and changing can help you increase your conversion rate.
Difference between prime cost and conversion cost
When you consider all the conversions that take place on your website, the conversion costs can include various factors. To calculate your expenses precisely , you need to have an overview of your paid marketing initiative. Bruce’s Bike Company is a bicycle manufacturer that specializes in high-end 10-speed bikes. Bruce is trying to figure out what his conversion costs are for the quarter in order to estimate his finished inventory for theinterim financial statements. The term conversion costs often appears in the calculation of the cost of an equivalent unit in a process costing system.
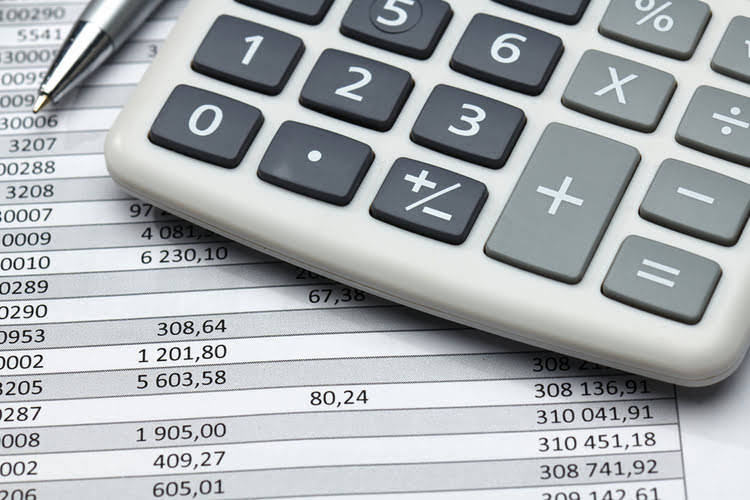
You could use that information as an inspiration to make changes and see if you can improve it. Calculating the conversion cost just involves simple division. To complete the calculation, you will need to know the number of conversions conversion costs made as a result of the campaign as well as the total spending on the campaign. You must know what the conversion cost formula is so that you must know about the spending, PPC ROI and wastages happening in campaigns.
Total Period Cost Formula
Marginal CostingMarginal costing in economics and managerial accounting refers to an increase or decrease in the total cost of production due to a change in the quantity of the desired output. It is variable, depending on the inclusion of resources required to produce or deliver additional unit of a product or service. Notice that the costs against items H, I and J have not been made part of any of prime cost or conversion cost computations.
The 5A uses only packaging sleeves as its direct material, while other types may also include nylon, felt, and/or the ingredients for the proprietary handgrip. Direct labor and manufacturing overhead are used to test, weigh, and sound-match the drumsticks into pairs. In the Peep-making process, the direct materials of sugar, corn syrup, gelatin, color, and packaging materials are added at the beginning of steps 1, 2, and 5. While the fully automated production does not need direct labor, it does need indirect labor in each step to ensure the machines are operating properly and to perform inspections . Prime cost calculation is important to determine the actual input costs involved in manufacturing.
How to Calculate Variable Contribution Margin
Remember that you can define conversion however you want, such as the number of sales and number of signups for your email list. The following are some of the most commonly used conversion metrics when calculate conversion cost. Each has its own example of how you would calculate conversions with your given definition for the conversions. If you divide the Total cost of generating traffic by the total number of conversions, you get the cost per conversion . It is used commonly in manufacturing units like paper, steel, soaps, medicines, vegetable oils, paints, rubber, and chemicals. Costs IncurredIncurred Cost refers to an expense that a Company needs to pay in exchange for the usage of a service, product, or asset.
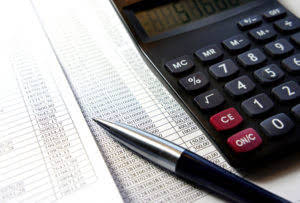
During June, Excite Company’s prime cost was $325,000 and conversion cost was $300,000. It is easier to track the materials and conversion costs for one batch and have those costs follow the batch to the next process. The costs of the employees who make the goods are known as direct labor expenses. Wages, worker insurance expenses, pension fund payments, bonuses, and any other expenditures linked with the hired workers participating in the manufacturing process are all examples of this. Managers and other supervisors can use conversion costs to properly assess and track production costs.
THE CRITICAL ROLE OF CONVERSION COST AND COMPARATIVE ADVANTAGE IN MODELING AGRICULTURAL LAND USE CHANGE
Direct labor costs are the wages paid to the employees engaged in manufacturing a product or provision of service. For example, wages or salary paid to the workers at the shop floor environment come under direct labor costs. A shop floor is the production area where people work on machines. Manufacturing overheads are the indirect costs incurred while manufacturing a product. In other words, prime costs are the direct materials and direct labor costs incurred in the manufacturing process.
The $50,000 paid to the production manager is manufacturing overhead, which is a conversion cost. The $200,000 cost for renting the production facility is part of manufacturing overhead costs, which are conversion costs. The $20,000 cost for utilities and insurances related to production are also manufacturing overhead, which are production costs. In a processing environment, there are two concepts important to determining the cost of products produced. These are the concepts of equivalent units and conversion costs. As you have learned, equivalent units are the number of units that would have been produced if one unit was completed before starting a second unit.
Is salary fixed or variable cost?
If you pay an employee a salary that isn’t dependent on the hours worked, that’s a fixed cost. Other types of compensation, such as piecework or commissions are variable. Annual salaries are fixed costs but other types of compensation, such as commissions or overtime, are variable costs.
For service organizations, cost of goods sold may be referred to as Cost of Services. This typically includes the cost of direct labor and manufacturing overhead (e.g. indirect materials, utility costs, depreciation, etc.). Calculating equivalent units and unit costs by adding direct labor and manufacturing overheads is more time-saving than calculating the two costs separately.
Universityجامعة الشارقة
In production/ manufacturing as it considers only two elements – direct labour and overheads. Prime cost is primarily impacted by two factors that are issues related to materials supply chain and issues direct labor and its efficacy.
What is the difference between COGS and expenses?
The difference between these two lines is that the cost of goods sold includes only the costs associated with the manufacturing of your sold products for the year while your expenses line includes all your other costs of running the business.
Know your target conversion cost and the current conversion rate. And keep these numbers in mind while getting rid of a keyword. So, make sure you make good use of these action words in your ad copy. And it will increase your conversion rate and reduce the conversion cost. For now, let’s move on to the importance of calculating conversion cost. And after that, we will share some tips with you to reduce your conversion cost. These factors include the industry and your product or service.
It tells you where to spend the money and where not to, which becomes even more critical for small and medium-sized businesses. And if you keep a tab on the conversion cost, you can make meaningful and timely changes to these campaigns. After all, how else can a company know if its marketing efforts are in the right direction? Conversion cost or cost per conversion is one such marketing metric.

Prime costs refer to expenses that are directly attributable to a product. This refers to all forms of compensation that the business pays its employees who are directly involved in the production of goods. Even if you fully automate your production process, there’s still the involvement of machinery and equipment. Although it will depend on how you choose to define conversions, most of the time, that term applies to the number of sales made. If you wanted to count it as a single interaction, you could instead use the cost of acquisition, with acquisition referring to each new customer. As with many other metrics, this model depends on the industry and the final product.
Companies that produce inventory rely heavily on certain metrics to track production as well as to evaluate the efficiency of how inventory is produced and sold. One of the metrics commonly used to do this is conversion costs. Examples of manufacturing overhead include the utilities, indirect labor, repairs and maintenance, depreciation, etc. that is occurring within a company’s manufacturing facilities. Is another costing term that quantifies the value of direct material, direct labor, and other direct expenses incurred in manufacturing any particular product. All prime costs have a direct one-to-one relation with products manufactured and can be directly traced to a specific product or products. For example, for a garment manufacturer, the quantum and cost of nova88 fabric used and man-hours and machine hours required to produce each type of garment can be specifically identified. Conversion costs, as the name implies, are all costs that must be incurred so as to transform raw materials into finished goods.
Why Should You Know How to Compute Conversion Cost?
Prime costs are mainly used to reassure managers about product pricing. The greater the ratio of prime costs over total costs the higher the chance a firm’s product cost accuracy is. This is because manufacturing overhead can’t be directly traced to any one product and must be allocated. Often the allocation of manufacturing overhead is inaccurate or misleading and can result in poor product pricing which leads to decreased profitability and poor decision-making. Prime costs include the expenses that directly relate to creating finished products.